Thực tiễn áp dụng “mô hình năng suất tổng thể” tại doanh nghiệp
Việc áp dụng mô hình năng suất tổng thể đã giúp Công ty TNHH Quang Quân tối đa hóa hiệu suất thiết bị, giảm tồn bán thành phẩm, giảm sản phẩm lỗi hỏng cũng như thời gian sản xuất, vận chuyển sản phẩm. Từ đó, nâng cao chất lượng sản phẩm, đáp ứng nhu cầu của khách hàng và dần khẳng định uy tín và lợi thế cạnh tranh trên thị trường.
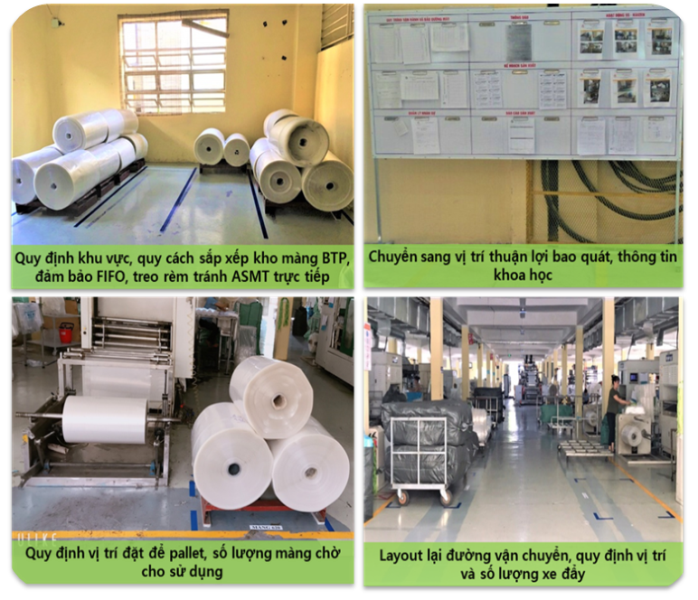
Nỗ lực cải tiến và kết quả đạt được
Công ty TNHH Quang Quân chuyên sản xuất các sản phẩm nhựa dùng một lần. Với phương châm giá cả hợp lý, phục vụ tận tình, Công ty đã dần khẳng định vị thế trên thường trường.
Tuy nhiên, như nhiều doanh nghiệp khác, trong bối cảnh mới, Công ty TNHH Quang Quân cũng gặp không ít những khó khăn, thách thức. Ngoài việc duy trì và phát triển thị trường nội địa, mục tiêu hướng tới thị trường quốc tế và sản phẩm mới đòi hỏi hệ thống quản lý của Công ty phải có sự đổi mới và cải tiến, tạo sự an tâm, tin tưởng cho khách hàng.
Để ứng phó với những thách và phát triển bền vững, Công ty TNHH Quang Quân đã tham gia Chương trình thí điểm “Áp dụng mô hình tổng thể cải tiến năng suất và chất lượng” của Bộ Công Thương.
Cùng với đẩy mạnh đổi mới, cải tiến quy trình sản xuất, Công ty TNHH Quang Quân cũng tăng cường tối ưu hoá các giải pháp hoạt động sản xuát; ban hành kế hoạch, quy định; thực hiện sàng lọc, tiêu chuẩn hóa các thiết bị trong nhà xưởng; xây dựng mô hình hệ thống quản lý chất lượng; phân chia khu vực thực hiện hoạt động tự quản nhằm nâng cao ý thức tự quản theo khu vực sản xuất và duy trì môi trường 5S…
Nhà máy Hà Nam (Khu công nghiệp Đồng Văn 1, Hà Nam) được Công ty TNHH Quang Quân chỉ định tổ chức thí điểm áp dụng mô hình. Đánh giá tình hình thực tế hoạt động sản xuất tại Nhà máy Hà Nam trước khi áp dụng mô hình tổng thể cải tiến năng suất và chất lượng, các chuyên gia tư vấn cho biết: Dòng chảy dây chuyền sản phẩm tại xưởng nắp ly chưa được tối ưu, thiết bị máy móc không được vệ sinh thường xuyên gây ra lỗi sản phẩm.
Theo ghi nhận của các chuyên gia, Công ty TNHH Quang Quân chưa áp dụng 5S vào sản xuất; hệ thống kiểm soát chất lượng của Công ty cũng chưa được thiết lập. Kỹ năng quản lý của đội ngũ quản đốc, quản lý cấp trung còn tương đối thấp; điểm hài lòng của nhân viên tại công ty thấp hơn so với mức trung bình của doanh nghiệp Việt Nam…
Nhằm hạn chế những tồn tại trên, các chuyên gia đề xuất Công ty TNHH Quang Quân áp dụng mô hình tổng thể cải tiến năng suất và chất lượng vào trong quá trình sản xuất bằng cách chuyển các khuôn máy đang chạy đặt gần nhau; bố trí đúng từng loại màng đặt ngay sau máy; các máy cùng loại gần nhau dùng chung xe vận chuyển thành phẩm. Nhờ đó, đã giảm được 33% quãng đường vận chuyển dòng chảy sản phẩm; giảm lượng xe vận chuyển thành phẩm từ 9 xuống còn 5 xe (giảm 45%).
Cùng với đó, để giảm lượng tồn bán thành phẩm nắp ly, nhóm cải tiến của Công ty TNHH Quang Quân đã giới hạn số lượng bán thành phẩm sản xuất ra từng ngày, xây dựng tiêu chuẩn sử dụng số lượng màng theo ngày. Kết quả, giảm tồn bán thành phẩm màng nắp ly 112 cuộn còn 46 cuộn/ngày (giảm 40%), giảm 50% diện tích mặt bằng sử dụng để lưu trữ màng nắp ly.
Đặc biệt, để nâng cao hiệu suất mát hút, nhóm cải tiến của Công ty đã giảm thời gian thay khuôn bằng cách chuẩn bị vật tư trước, vệ sinh khuôn sạch sẽ và đặt ngay gần máy, 2 người 2 bên máy thay khuôn. Kết quả, giảm 50% thời gian thay khuôn máy hút từ 30 phút xuống còn 15 phút….
Tối ưu hoá các giải pháp
Cùng với đẩy mạnh đổi mới, cải tiến quy trình sản xuất, Công ty TNHH Quang Quân cũng tăng cường tối ưu hoá các giải pháp hoạt động sản xuất; ban hành kế hoạch, quy định; thực hiện sàng lọc, tiêu chuẩn hóa các thiết bị trong nhà xưởng; xây dựng mô hình hệ thống quản lý chất lượng; phân chia khu vực thực hiện hoạt động tự quản nhằm nâng cao ý thức tự quản theo khu vực sản xuất và duy trì môi trường 5S… Cụ thể:
- Tối ưu hóa bằng cách giảm quãng đường vận chuyển màng nắp ly: Sau khi đặt các khuôn máy chạy đặt gần nhau, bố trí đúng từng loại màng đặt ngay sau máy đồng thời các máy cùng loại gần nhau dùng chung xe vận chuyển thành phẩm, đã giảm đường vận chuyển dòng chảy sản phẩm từ 120m xuống còn 90m (giảm 33%); giảm lượng xe vận chuyển thành phẩm từ 9 xe xuống còn 5 xe (giảm 45%).
- Giảm lượng tồn bán thành phẩm nắp ly bằng cách cân bằng sản xuất các công đoạn: Dựa vào sơ đồ phân tích chuỗi giá trị và theo kế hoạch sản xuất năm, số lượng bán thành phẩm sản xuất ra từng ngày được giới hạn, đồng thời phỏng vấn thực tế công nhân máy về số lượng màng theo từng ca để xây dựng tiêu chuẩn sử dụng số lượng màng theo ngày. Kết quả giảm tồn bán thành phẩm màng nắp ly từ 112 cuộn xuống còn 46 cuộn/ngày (giảm 40%), giảm 50% diện tích mặt bằng sử dụng để lưu trữ màng nắp ly.
- Nâng cao hiệu suất máy hút bằng cách giảm thời gian thay khuôn: Các vật tư được chuẩn bị trước, vệ sinh khuôn sạch sẽ và đặt ngay gần máy, 2 người 2 bên máy thay khuôn đã giúp giảm thời gian thay khuôn máy hút từ 30 phút xuống còn 15 phút.
- Giảm lỗi công đoạn máy nắp ly bằng cách vệ sinh đường ống nước làm mát: Sau khi tìm ra nguyên nhân gốc rễ gây ra tỷ lệ 5% lỗi màng xấu, mỏng của máy nắp ly là nước máy làm mát bẩn và dao máy băm cùn, nhóm cải tiến đã cho công nhân vệ sinh hệ thống máy làm mát và thay dao mới, giúp giảm tỷ lệ màng xấu, mỏng từ 5% xuống còn 3,7% (giảm 26%), tỷ lệ thành phẩm tăng 0,5%.
- Thực hành tốt 5S, cải thiện môi trường làm việc: Nhà máy được thực hiện vệ sinh và tổng vệ sinh định kỳ; Thực hiện sàng lọc, tiêu chuẩn hóa các thiết bị trong nhà xưởng.
- Tuân thủ các quy cách đặt để, đúng vị trí, đúng số lượng: Đánh dấu vị trí đặt để của từng khu vực, công cụ; bố trí sắp xếp hợp lý nhà xưởng, giảm quãng đường di chuyển, ban hành quy định sắp xếp, vận chuyển cho từng khu vực, công cụ.
- Về mặt hệ thống quản lý chất lượng: Xây dựng mô hình hệ thống quản lý chất lượng từ mô hình kiểm tra chất lượng sản phẩm sang mô hình quản lý chất lượng; xây dựng quy trình công đoạn trọng tâm máy trộn và máy hút, xây dựng bảng phân tích và hướng dẫn công việc đóng gói sản phẩm tại xưởng nắp ly và thiết kế bàn kiểm tra chất lượng đầu ra.