Áp dụng công cụ LEAN vào sản xuất - Chìa khóa thành công của một doanh nghiệp cơ khí
Nhờ xác định rõ nguyên nhân gây lãng phí trong các công đoạn sản xuất, Công ty Cổ phần Cơ khí Quang Minh đã triển khai áp dụng thành công công cụ thực hành LEAN vào dây chuyền sản xuất; qua đó, nâng cao năng suất lao động và tiết kiệm chi phí sản xuất thông qua việc loại bỏ các lãng phí ở một số công đoạn sản xuất của công ty này.
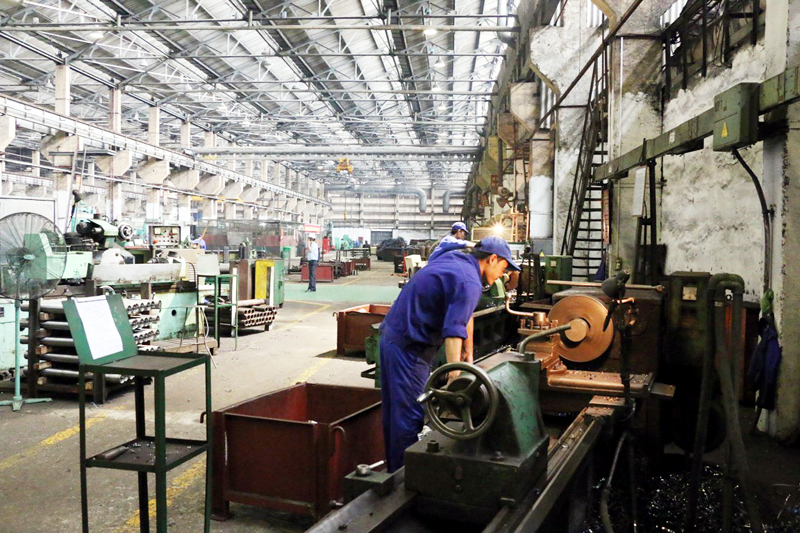
Nhận diện những lãng phí trong các công đoạn sản xuất
Công ty Cổ phần Cơ khí Quang Minh (Công ty Quang Minh) chuyên tư vấn thiết kế, chế tạo, cung cấp, lắp đặt và chuyển giao công nghệ trong các ngành bia, rượu, sữa, nước giải khát, hoá chất, mỹ phẩm, vi sinh và công nghệ thực phẩm…
Sản phẩm của Công ty được phân phối tiêu thụ tại một số thị trường chính như: Miền Tây, miền Trung, miền Bắc; tại TP. Hồ Chí Minh; tại nước ngoài là Pnompenh - Campuchia và tại Philippinnes. Công ty Quang Minh là một trong số các doanh nghiệp (DN) tham gia Chương trình quốc gia “Nâng cao năng suất và chất lượng sản phẩm, hàng hóa của DN Việt Nam đến năm 2020”.
Qua nhiều lần khảo sát thực tiễn sản xuất và họp bàn với Ban lãnh đạo Công ty Quang Minh, các chuyên gia của Trung tâm Tiêu chuẩn Đo lường Chất lượng 3 (QUATEST 3) đã phân tích và chỉ ra cho Ban lãnh đạo Công ty những công đoạn sản xuất gây lãng phí thời gian, năng suất chất lượng của sản phẩm.
Cụ thể, những lãng phí trong sản xuất được chỉ ra ở những công đoạn sau: Lãng phí từ các thao tác thừa, tốn nhiều thời gian tìm kiếm vật tư, công cụ phục vụ cho sản xuất. Hầu hết các thiết bị, dụng cụ trong Công ty từ đồ đạc, công cụ, dụng cụ, vật tư, nguyên liệu chưa được sắp xếp theo một trật tự; kho vật tư bừa bộn; có rất nhiều thiết bị, đồ vật không cần thiết, không phục vụ cho công việc sản xuất nhưng lại chiếm nhiều diện tích.
Ngoài các lãng phí trên, trong công đoạn sản xuất của Công ty Quang Minh còn có những lãng phí khác như: Lỗi về thẩm mỹ các đường hàn; năng suất ở một số công đoạn còn thấp, do sử dụng nhân lực nhiều, có nhiều thao tác thừa. Thời gian tạo ra giá trị cho sản phẩm không cao, trong khi đó thời gian cho các hoạt động không tạo ra giá trị lại nhiều.
LEAN - “phao cứu sinh” nâng cao năng suất cho Công ty Quang Minh
Để loại bỏ những lãng phí và ghi nhận được kết quả trong hoạt động sản xuất, DN này đã áp dụng và triển khai thành công công cụ LEAN. Sau khi áp dụng công cụ LEAN vào các công đoạn sản xuất đã giúp Công ty Quang Minh nâng cao năng suất lao động và tiết kiệm chi phí sản xuất.
Từ những hiệu quả thiết thực mà công cụ LEAN mang lại, Ban lãnh đạo Công ty Quang Minh đã tiếp tục áp dụng công cụ LEAN và phát động hoạt động cải tiến để loại bỏ các lãng phí, nâng cao hiệu quả sản xuất kinh doanh của Công ty.
Theo QUATEST 3, việc xác định các nguyên nhân gây lãng phí trong các công đoạn sản xuất tại Công ty Quang Minh có ý nghĩa hết sức quan trọng. Bời vì, khi nhận diện rõ các yếu tố lãng phí tác động đến các công đoạn sản xuất sẽ giúp Ban lãnh đạo Công ty nhìn nhận, đánh giá lại các quy trình, công đoạn sản xuất có phù hợp với hoạt động của DN mình không?.
Trả lời câu hỏi trên, Công ty Quang Minh đã hợp tác với các chuyên gia của QUATEST trong việc áp dụng công cụ thực hành cải tiến 5S và công cụ Kaizen trong phạm vi toàn Công ty. Theo đó, các chuyên gia của QUATEST đã tiến hành đào tạo kiến thức 5S cho toàn bộ cán bộ, công nhân viên của Công ty; Thực hiện Sàng lọc, loại bỏ các đồ vật không cần thiết; Thực hiện Sắp xếp, tiêu chí Dễ thấy - Dễ lấy – Dễ kiểm - Dễ trả lại; Thực hiện Sạch sẽ, phân công trách nhiệm vệ sinh chi tiết ở từng tổ, khu vực; Thực hiện Săn sóc: Thành lập ban 5S nhằm Tổ chức đánh giá 5S định kỳ hằng tháng nhằm phát hiện vấn đề và liên tục cải tiến; Ban hành quy chế thực hiện 5S.
Ngoài việc áp dụng thực hiện 5S, Công ty còn áp dụng công cụ thực hành Kaizen để nhận diện các lãng phí, từ đó loại bỏ các lãng phí trong các công đoạn sản xuất. Công ty đã áp dụng Kaizen để cải tiến phương pháp ra tole, chuyển từ rat tole thủ công sang ra tole bằng thiết bị (ước tính tiết kiệm chi phí 6 triệu đồng/tháng); cải tiến phương pháp cẩu hạ thân tole, giữ nguyên được mép tole không bị khuyết tật khi hạ thân tole (ước tính tiết kiệm chi phí 3.484.000 triệu đồng/tháng); Cải tiến phương pháp rút lỗ trên thân tank, nhờ đó chất lượng lỗ đồng đều (ước tính tiết kiệm chi 774.000 đồng/tháng).
Bên cạnh đó, Kaizen cũng giúp cải tiến phương pháp đánh bóng đáy côn, chuyển từ đánh bóng thủ công sang đánh bằng máy, độ bóng bề mặt đồng đều hơn (ước tính tiết kiệm chi 11.400.000 đồng/tháng…).
Như vậy, có thể thấy, việc áp dụng các công cụ LEAN vào các công đoạn sản xuất của Công ty Quang Minh đã góp phần nâng cao năng suất lao động và tiết kiệm chi phí sản xuất thông qua việc loại bỏ các lãng phí trong một số công đoạn sản xuất.
Theo QUATEST 3, việc xác định các nguyên nhân gây lãng phí trong các công đoạn sản xuất tại Công ty Quang Minh có ý nghĩa hết sức quan trọng. Bời vì, khi nhận diện rõ các yếu tố lãng phí tác động đến các công đoạn sản xuất sẽ giúp Ban lãnh đạo Công ty nhìn nhận, đánh giá lại các quy trình, công đoạn sản xuất có phù hợp với hoạt động của DN mình không?. Trả lời câu hỏi này, Công ty Quang Minh đã hợp tác với các chuyên gia của QUATEST trong việc áp dụng công cụ thực hành cải tiến 5S và công cụ Kaizen trong phạm vi toàn Công ty.