Công cụ LEAN hỗ trợ tích cực cho các doanh nghiệp trong quản lý tinh gọn
Thời gian qua, nhiều doanh nghiệp (DN) đã áp dụng thành công công cụ quản lý tinh gọn LEAN vào các quy trình sản xuất của đơn vị, qua đó giúp DN tiết kiệm được nhiều chi phí sản xuất, nâng cao năng suất và chất lượng sản phẩm, tạo ra sự đột phá trong sản xuất.
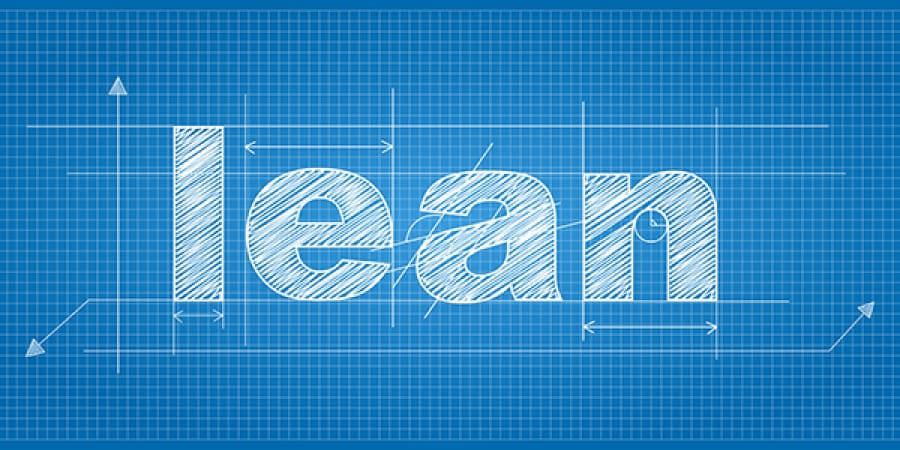
Được thành lập từ năm 1990, Xí nghiệp Thức ăn Chăn nuôi Thuỷ sản An Giang là DN có nhiều thành tự trong lĩnh vực chế biến, sản xuất các sản phẩm chăn nuôi, thức ăn dành cho gia súc gia cầm và thuỷ sản.
Tuy nhiên, DN không tránh khỏi việc gặp phải một số tồn tại nhất định trong quá trình hoạt động, như: Lãng phí thao tác thừa do tốn thời gian tìm kiếm vật tư, công cụ dụng cụ phục vụ cho sản xuất; lãng phí liên quan đến dừng máy do sự cố máy móc thiết bị; lãng phí từ việc sử dụng chưa đúng hiệu suất máy móc thiết bị dẫn đến việc giảm năng suất chất lượng cũng như nhận về những phản hồi tiêu cực từ đối tác, khách hàng,…
Để khắc phục điều này, Ban lãnh đạo Xí nghiệp đã quyết định tham gia Chương trình phương pháp Sản xuất tinh gọn LEAN do Chính phủ hỗ trợ, cùng với sự tư vấn và đồng hành của Trung tâm Kỹ thuật Tiêu chuẩn Đo lường Chất lượng 3 (QUATEST 3).
Sau một thời gian thí điểm các công cụ TPM (kiểm soát và tối đa hiệu suất sử dụng máy móc, thiết bị) và AM (công cụ bảo trì tự quản) của LEAN tại dây chuyền sản xuất, khối văn phòng và kho bao bì vật tư của Xí nghiệp An Giang đã nhận được những kết quả tích cực.
Theo đó, nhiều sự cố nhỏ từ máy móc thiết bị đã được khắc phục, thiết bị đã được trả lại tình trạng “như mới”. Thiết bị luôn được chăm sóc nhờ sự phân công trách nhiệm rõ ràng: Làm gì? Ai làm? Khi nào làm? Làm như thế nào? Ai kiểm tra việc thực hiện? Công nhân vận hành đã ý thức hơn về trách nhiệm của mình với máy móc thiết bị; Sự phối hợp trong chăm sóc thiết bị giữa công nhân vận hành & công nhân bảo trì nhịp nhàng hơn; Hiểu biết và kỹ năng xử lý sự cố nhỏ của công nhân vận hành được nâng cao.
Đối với Công ty TNHH Nệm Ưu Việt, tuy đã có thời gian hoạt động lâu năm (từ 1993), Công ty vẫn không tránh khỏi những bất cập trong quản lý và sử dụng nguồn nhân lực, gây ảnh hưởng trực tiếp đến năng suất và chất lượng sản phẩm, tạo ra những tổn thất không đáng có.
Sau khi áp dụng LEAN với các công cụ 5S, nhiều giải pháp đã giúp Công ty tiết kiệm 957 triệu đồng/năm. Vật tư, bán thành phẩm, dụng cụ máy may được sàng lọc, phân loại và sắp xếp gọn gàng, theo khu vực riêng.
Với mong muốn hướng tới sự phát triển hoàn hảo, tối ưu hóa hoạt động sản xuất, loại bỏ lãng phí, nâng cao năng suất, chất lượng, trong nhiều năm qua, Công ty TNHH Một thành viên Cơ khí Hà Nội (HAMECO) đã áp dụng và đạt được nhiều chứng chỉ đáp ứng các tiêu chuẩn như ISO 9001:2015, ISO 50001:2011… Cùng với đó, Công ty kết hợp công cụ 3D5S và đang đem lại những hiệu quả tương đối tốt trong quản lý và giảm thiểu một số lãng phí trong sản xuất liên quan đến việc tìm kiếm, quản lý kho.
Từ năm 2020, việc áp dụng LEAN tạo ra sự đột phá trong sản xuất tại HAMECO. DN đã triển khai dự án áp dụng sản xuất tinh gọn LEAN, nâng cao năng suất chất lượng cho dòng sản phẩm Đối trọng xe xúc - sản phẩm chiếm đến 60% tổng sản lượng của Công ty.
Bằng việc triển khai áp dụng 3 đề tài cải tiến, HAMECO đã thu được những kết quả tích cực, đạt được mục tiêu đề ra. Với sự cải tiến, bố trí lại mặt bằng và tối ưu lại quy trình sản xuất tại xí nghiệp đúc, thời gian đúc một sản phẩm đối trọng xe xúc giảm từ 23,5 giờ xuống còn 17,5 giờ, mức độ cải thiện 25,53%.
Thời gian sản xuất một sản phẩm đối trọng 3,5 tấn trước cải tiến 208 giờ (khoảng 26 ngày công), sau cải tiến 152 giờ (khoảng 19 ngày công), mức độ cải thiện 26,92%; chênh lệch so với thời gian nguyên công lý tưởng giảm từ 113% xuống còn 58%. Tổng quãng đường di chuyển giảm từ 4.000 mét xuống 2.800 mét (mức độ cải thiện 30%).
Tại Nhà máy Z113, sau 6 tháng nỗ lực, nhà máy đã nhận được những kết quả cải thiện rõ ràng. Khoảng cách vận chuyển bán thành phẩm giữa các tổ gia công được rút ngắn từ 146 mét trước khi cải tiến xuống còn 48 mét sau cải tiến; quãng đường vận chuyển giảm 98m. Việc cải thiện này có ý nghĩa rất lớn do sản lượng hàng năm khoảng 800 mũi khoan, mỗi mũi khoan nặng khoảng 19kg.
Thời gian hoàn thành một sản phẩm tại công đoạn gia công biên dạng ngoài của chóp mũi khoan xoay cầu cải thiện được khoảng 9% thời gian gia công; Giảm được công sức cho người lao động khi di chuyển phôi và thành phẩm (nặng khoảng 19 kg/sản phẩm). Quá trình chuyển đổi tại công đoạn gia công mảnh thân mũi khoan xoay cầu đã giảm được khoảng 14%.