Kinh nghiệm áp dụng thành công Lean trong ngành Cơ khí
Áp dụng thành công sản xuất tinh gọn (Lean) đã và đang giúp nhiều doanh nghiệp cơ khí cải tiến và nâng cao năng suất, chất lượng, đúc kết ra nhiều kinh nghiệm, bài học thực tiễn quý báu.
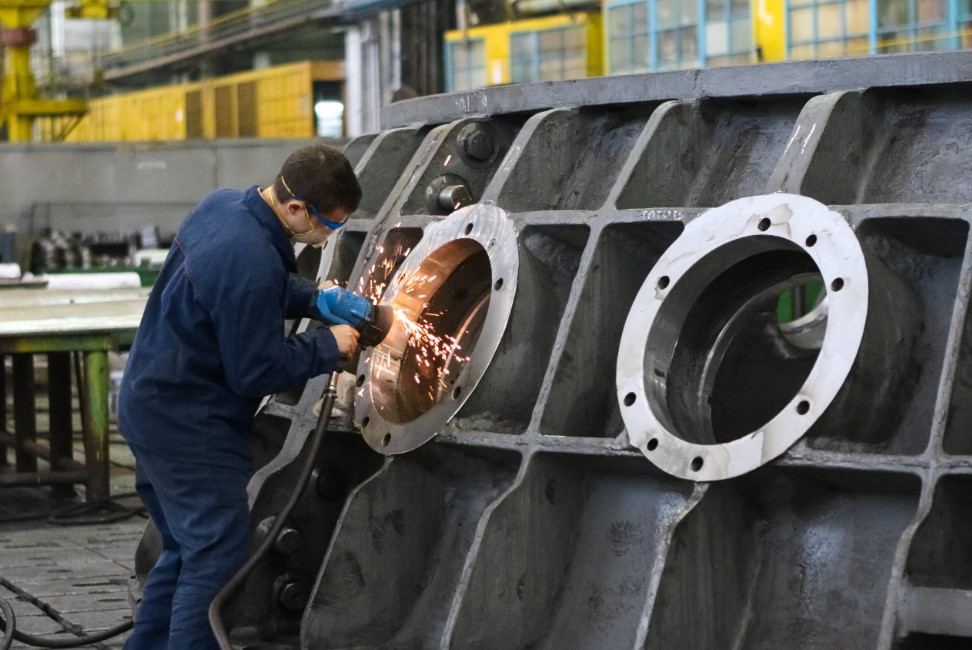
Thay đổi quan điểm sản xuất của người lao động
Theo các chuyên gia lĩnh vực năng suất, chất lượng, bài học đầu tiên là doanh nghiệp cần xác định rõ các lãng phí. Thực tế cho thấy, hệ thống quản lý sản xuất của doanh nghiệp cơ khí chế tạo Việt Nam hiện tồn tại nhiều hạn chế và lãng phí.
Theo đó, có thể chỉ ra một số lãng phí phổ biến là: Lãng phí do sản xuất lỗi; lãng phí do sản xuất thừa; lãng phí do tồn kho thành phẩm hoặc bán thành phẩm; lãng phí do các động tác thừa; lãng phí thời gian do chờ đợi hay trì hoãn; lãng phí về vận chuyển hay di chuyển.
Trong giai đoạn đầu áp dụng hệ thống sản xuất Lean và thực hiện một số cải tiến vào hệ thống quản lý sản xuất, doanh nghiệp có thể nhanh chóng loại bỏ một phần lãng phí này, song khó có thể loại bỏ hoàn toàn.
Mô hình sản xuất tinh gọn sẽ giúp giảm thiểu các lãng phí này một cách hiệu quả nhất và liên tục được cải tiến, thực hiện nhằm dần loại bỏ hoàn toàn các lãng phí.
Bài học thứ hai là thay đổi quan điểm sản xuất của người lao động. Một số hoạt động cơ bản nhằm thay đổi quan điểm của người lao động về sản xuất tinh gọn gồm: Tổ chức các buổi đào tạo, thảo luận và thực hành trong sản xuất; đưa ra các hình ảnh, clip ví dụ thành công từ các doanh nghiệp khác.
Bên cạnh đó, khuyến khích người lao động tham gia vào quá trình cải tiến, bao gồm phát hiện vấn đề, đưa ra các cải tiến để khắc phục và cùng với người lao động thực hiện những cải tiến đó.
Giúp người lao động hiểu rằng việc áp dụng Lean sẽ giúp công ty nâng cao năng lực cạnh tranh, mang lại lợi ích và giá trị gia tăng cho công ty, đồng nghĩa với lợi ích của người lao động.
Bài học thứ ba là lựa chọn công cụ phù hợp. Lean có nhiều công cụ. Để lựa chọn được công cụ nào là phù hợp với từng công ty cụ thể cần dựa trên một số đặc điểm sau: Quy mô và đặc điểm, hiện trạng hoạt động, sản xuất của từng công ty.
Nghiên cứu, phân loại những lãng phí và cơ hội cần cải tiến từ đó có thể chọn lựa được các công cụ thích hợp để giải quyết; cùng với lãnh đạo doanh nghiệp, quản lý cấp trung bàn bạc, thảo luận và đưa ra các phương án cải tiến.
Nên bắt đầu áp dụng Lean với quy mô nhỏ, trước khi áp dụng cho toàn bộ hoạt động sản xuất của công ty.
Cần duy trì cải tiến liên tục
Bài học thứ tư là huấn luyện về Lean và các công cụ cải tiến. Khi triển khai dự án, cần đào tạo sâu về Lean và các công cụ cải tiến cho các cấp quản lý doanh nghiệp.
Đồng thời, hỗ trợ doanh nghiệp tổ chức các lớp đào tạo, thay đổi nhận thức cho công nhân về quản lý sản xuất tinh gọn; thông qua đào tạo, huấn luyện, thuyết phục người lao động nhận thức về lợi ích khi áp dụng sản xuất Lean.
Bài học quan trọng thứ năm là duy trì cải tiến liên tục. Đặc thù của cải tiến, đặc biệt là trong ngành cơ khí chế tạo, là không chỉ giải quyết một lần mà vấn đề lãng phí sẽ bị loại bỏ tận gốc, mà cần thực hiện hoạt động cải tiến liên tục, nhằm dần loại bỏ triệt để vấn đề lãng phí.
FOMECO là thành viên của Tổng công ty Máy động lực và máy nông nghiệp Việt Nam (VEAM). Nhà máy có tổng diện tích 172.000 m2, diện tích dành cho nhà xưởng của các xí nghiệp khoảng 90.000 m2. FOMECO đầu tư trang bị nhiều thiết bị, phân bố cho các xí nghiệp dựa theo quy trình sản xuất riêng của từng xí nghiệp.
Bên cạnh việc đầu tư mạnh vào trang thiết bị, dây chuyền hiện đại, tự động hóa, doanh nghiệp này đã áp dụng hàng loạt các hệ thống quản lý theo tiêu chuẩn ISO 9001:2015, ISO 50001:2011, ISO IATF 16949:2016, ISO 14001:2015 và chú trọng việc nghiên cứu và áp dụng các công cụ cải tiến năng suất chất lượng, điển hình như áp dụng Lean..
FOMECO đã lựa chọn được 3 đề tài cải tiến bao gồm: Bố trí lại mặt bằng khu vực sản xuất cần khởi động; tối ưu hóa các thao tác kết hợp quản lý trực quan; thực hiện cải tiến Kaizen tại một số công đoạn.
Sau nhiều tháng nỗ lực và được sự đồng lòng của toàn bộ công nhân viên thuộc nhóm cải tiến và sản xuất cần khởi động, các lãng phí đã được loại bỏ. Cụ thể, tổng quãng đường di chuyển giảm 47%, kéo theo thời gian cho hoạt động di chuyển trong sản xuất giảm 36,5%.
Bên cạnh đó, việc cải tiến trực quan hóa tiêu chuẩn thao tác làm việc cũng hỗ trợ rất nhiều cho việc tăng chất lượng làm việc của công nhân, giảm thao tác thừa. Đồng thời, việc đào tạo công nhân mới dễ dàng và hiệu quả hơn…
Một trong những bí quyết thành công của doanh nghiệp này là có nguồn lực mạnh mẽ cùng quyết tâm, sự cam kết rất cao từ Ban Lãnh đạo trong việc áp dụng Lean cải thiện hiệu quả sản xuất.
Lãnh đạo Công ty quyết tâm duy trì áp dụng Lean, tiếp tục áp dụng sản xuất tinh gọn cho các hoạt động sản xuất khác, loại bỏ các chi phí phát sinh do lãng phí, nâng cao hiệu quả sản xuất.