Hưởng quả ngọt nhờ áp dụng mô hình tổng thể cải tiến năng suất và chất lượng
Nhờ sớm áp dụng mô hình tổng thể, nhiều doanh nghiệp đã và đang hưởng quả ngọt trong việc nâng cao năng suất và chất lượng hàng hóa.
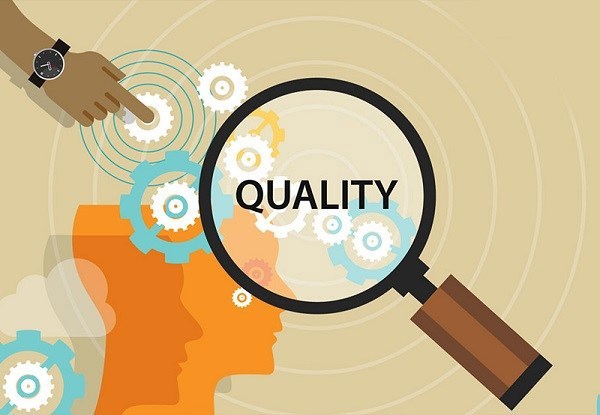
Vì sao cần áp dụng mô hình này?
Theo các chuyên gia năng suất, hiểu một cách đơn giản thì việc áp dụng mô hình tổng thể cải tiến năng suất và chất lượng chính là việc phát triển tổ chức định hướng khách hàng; liên tục cải tiến và đổi mới công nghệ; tổ chức quản lý sản xuất hiệu quả; giảm lãng phí trong quá trình sản xuất và cung cấp dịch vụ…
Tuy nhiên, tùy thuộc vào đặc thù từng ngành, vai trò của các yếu tố trong mô hình nâng cao năng suất chất lượng tổng thể sẽ có thể khác nhau. Dựa trên nền tảng mô hình căn bản, nhưng khi vận dụng sẽ linh hoạt cho từng doanh nghiệp.
Tùy vào văn hóa và loại hình sản phẩm mà doanh nghiệp sẽ thiết kế mô hình phù hợp với doanh nghiệp mình nhưng vẫn cần dựa trên trụ cột và nền tảng của mô hình chung. Các công cụ cải tiến năng suất, chất lượng sẽ được sử dụng như các phương tiện để đạt tới mục tiêu của từng trụ cột trong mô hình.
Doanh nghiệp thuộc mỗi ngành kinh tế có những đặc điểm, năng lực và năng suất lao động khác nhau. Đối với ngành nhựa năng lực sản xuất phần nhiều dựa trên thiết bị, công nghệ. Vì vậy, đầu tư phát triển công nghệ với hệ thống máy móc hiện đại, nâng cao trình độ của người lao động và áp dụng giải pháp quản lý tiên tiến giúp kỳ vọng cải tiến năng suất một cách đáng kể.
Cụ thể, việc phát triển tổ chức định hướng khách hàng được hiểu là phải bắt đầu với việc hiểu rõ ai là khách hàng của mình, họ cần gì, tại sao họ lại cần tới những sản phẩm đó, làm thế nào họ sử dụng được và với mức giá nào họ sẵn sàng chi trả để mua sản phẩm. Những nhu cầu và mong muốn của khách hàng phải được xem xét khi sản xuất các sản phẩm và dịch vụ. Toàn bộ hệ thống hay quá trình sản xuất của doanh nghiệp cần gắn liền với mục tiêu chiến lược này.
Hay như cải tiến và đổi mới công nghệ chính là việc áp dụng các kỹ thuật tiên tiến và máy móc hiện đại vào sản xuất để rút ngắn thời gian cũng như quy trình sản xuất mà sản phẩm lại ít lỗi. Đây là hướng đi mà các doanh nghiệp bắt buộc phải lựa chọn nếu muốn cạnh tranh được trong nền kinh tế hiện nay…
Và thành công của doanh nghiệp
Được biết đến là một trong những công ty nhựa hàng đầu ở Việt Nam, nhiều năm qua Công ty TNHH Sản xuất – Thương mại Nhựa kỹ thuật VINASTAR đã xây dựng một chiến lược chuyển đổi năng suất rất cụ thể và hiệu quả.
Theo đó, trên cơ sở tư vấn của các chuyên gia đến từ Viện Năng suất Việt Nam, các nhóm cải tiến năng suất chất lượng được thiết lập tại công ty VINASTAR gồm 5 nhóm: Cải tiến hiệu suất thiết bị; Cải tiến tiến độ giao hàng; Cải tiến chất lượng nâng cao sự thỏa mãn của khách hàng; Nhận biết và giảm lãng phí trong phân xưởng; Nâng cao hiệu suất làm việc thông qua bộ chỉ số KPI.
Cụ thể, Công ty đã thực hiện tính toán sát hơn thời gian chu kỳ để lập kế hoạch. Lập kế hoạch sản xuất liên tục hơn cho đơn hàng để giảm thời gian lên xuống khuôn, thông báo lịch sản xuất sớm cho khâu phối trộn. Theo dõi sản lượng sản xuất liên tục hơn để thông báo phối trộn nguyên liệu đúng tiến độ sản xuất. Công ty cũng nghiên cứu tự động hóa, đầu tư robot, cải tiến khâu đổ nguyên liệu vào máy…
Đặc biệt, lên kế hoạch cho mọi khâu liên quan đến khuôn để bộ phận khuôn có thể chủ động thay vì bị động như hiện nay. Đối với giải pháp cải tiến công nghệ, thiết bị, Công ty đã đưa ra 3 giải pháp chủ chốt bao gồm: giảm số lần cấp liệu nhựa thủ công, giảm nhân công bằng cách sử dụng máy hút liệu cấp tự động. Tăng thể tích bồn chứa; giảm lỗi (NG) sản phẩm và khuôn bằng cách cải tiến thiết bị làm mát nhanh bằng tăng số đường làm mát; Tăng tự động hóa: Bố trí Robot gắp sản phẩm. Rút bớt được nhân lực, một công nhân sẽ phụ trách 2 máy thay vì phụ trách 1 máy như trước kia.
Bên cạnh đó, Công ty cũng áp dụng 4 giải pháp quản lý bao gồm xây dựng hệ thống dữ liệu về hiệu suất thiết bị, cập nhật và thông tin trên màn hình máy tính quản lý; xây dựng các hướng dẫn thiết bị, hướng dẫn kiểm tra một cách trực quan, giúp công nhân nhanh nắm bắt được công việc; xây dựng quy trình quản lý khuôn, đảm bảm chất lượng khuôn trước khi sản xuất; giảm thời gian thay khuôn, bảo dưỡng khuôn: chuẩn hóa khu vực để khuôn giảm thời gian tìm kiếm, vận chuyển khuôn. Sơn phân loại khuôn theo khách hàng.
Sau khi thực hiện nghiêm túc và bài bản các giải pháp trên, kết quả dễ nhận biết đầu tiên là nâng cao nhận thức của người công nhân. Thay vì ỷ lại vào bộ phận bảo trì, nay mỗi công nhân tự thực hiện vệ sinh và kiểm tra các khâu không cần thiết phải có sự hỗ trợ của bảo trì như: loại trừ tất cả bụi bẩn trên máy, tra dầu, siết ốc, vệ sinh và tự bảo dưỡng những khâu đơn giản cho máy móc thiết bị. Tiếp theo là nâng cao vai trò và năng lực chuyên môn của tổ cơ điện.
Từ đó thiết lập các chương trình đào tạo từ đơn giản đến phức tạp và chia sẻ kinh nghiệm cho công nhân lao động về sửa chữa và bảo dưỡng. Cải tiến các khu vực khó thâm nhập cho vệ sinh và tra dầu. Rút ngắn thời gian kiểm tra và tra dầu. Các kiến thức, kinh nghiệm về công nghệ, thiết bị được đưa vào các hướng dẫn vận hành, tiêu chuẩn bảo dưỡng, vệ sinh máy móc, thiết bị, được chuẩn hóa và áp dụng trên toàn Công ty.
Kết quả cho thấy chỉ số hiệu suất thiết bị toàn phần đã được tăng lên từ 59% lên 75%, đạt mức khá trong khối các doanh nghiệp sản xuất. Bên cạnh đó, Công ty cũng tiến hành các cải tiến giảm lãng phí.
Từ việc nhận diện được 7 lãng phí trong sản xuất, nhóm cải tiến đã tập trung xử lý các cải tiến giảm chi phí sửa chữa máy móc thiết bị; Cải tiến giảm lãng phí nhân sự; Cải tiến giảm lãng phí về công cụ, dụng cụ, văn phòng phẩm trong sản xuất; Cải tiến giảm lãng phí nguyên liệu; Cải tiến giảm lãng phí trong việc vận chuyển, lưu kho, bảo quản nguyên liệu, vật tư, sản phẩm…