Áp dụng TPM tạo ra hiệu quả tích cực trong sản xuất kinh doanh của doanh nghiệp
Khi các doanh nghiệp (DN) áp dụng công cụ TPM (bảo trì năng suất toàn diện), thời gian bảo trì, bảo dưỡng được vào kế hoạch sản xuất. Điều này giúp duy trì tất cả các thiết bị ở trạng thái tốt nhất, giảm thời gian chết, tránh sự cố và chậm trễ trong quá trình sản xuất của DN.
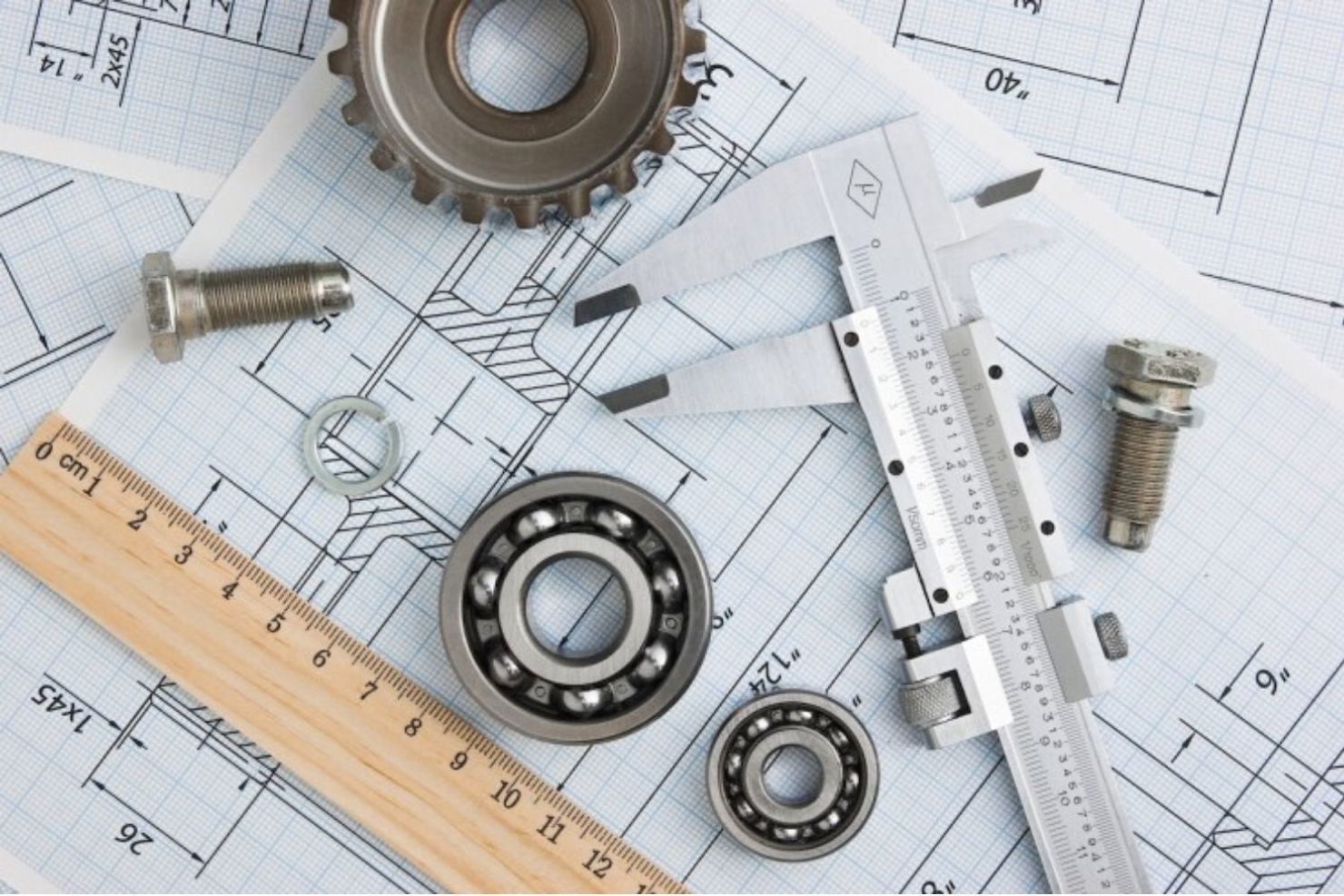
Mục tiêu tối thượng của phương pháp quản lý TPM là đảm bảo môi trường sản xuất không có bất kỳ sự cố cơ học và xáo trộn kỹ thuật nào, bằng cách trao nhiệm vụ bảo trì, bảo dưỡng định kỳ cho chính những người vận hành, quen thuộc nhất với thiết bị đó. Điều này giúp tiết kiệm thời gian, chi phí và tạo ra sự đột phá doanh thu cho DN.
Thực tế cho thấy, khi DN kiên trì áp dụng TPM, thì sẽ đạt được các mục tiêu quan trọng về năng suất (quản lý hệ thống sản xuất, kế hoạch sản xuất và thay thế phụ tùng, theo dõi các chỉ tiêu một cách chi tiết); Chất lượng sản phẩm chất lượng ngày càng cao; giảm chi phí phát sinh xuống mức thấp nhất; giao hàng nhanh nhất; nâng cao tinh thần làm việc của công nhân viên; Tạo dựng môi trường làm việc an toàn, thân thiện, tích cực...
Ngay từ những năm 2018-2019, Bộ Công Thương đã hỗ trợ cho 24 DN điển hình áp dụng công cụ TPM. Các hoạt động chính đã được triển khai tại nhiều DN điển hình; xây dựng và duy trì các quy trình quản lý, bảo dưỡng thiết bị; đào tạo nội bộ hướng tới mục tiêu không phế phẩm, không sự cố dừng máy, không hao hụt và không tai nạn.
Các DN đã áp dụng công cụ TPM có thể kể đến như: Công ty TNHH Công nghiệp Trí Cường (TCI); Công ty TNHH MTV Động Cơ và Máy Nông Nghiệp Miền Nam (SVEAM); Trung tâm thiết bị ngân hàng Tân Huy Hoàng; Công ty cổ phần Sơn Hải Phòng; Công ty TNHH Cơ khí Duy Khanh; Công ty Cường Vinh… Sau một thời gian ngắn áp dụng TPM, nhiều DN đã có những cải tiến đáng kể.
Đối với công ty Cường Vinh, khi áp dụng công cụ cải tiến TPM, DN này đã giảm 5,8% thời gian dừng máy và nâng cao hiệu quả sản xuất tại phân xưởng đúc nhôm. Từ tháng 10/2018, Công ty đã thành lập ban TPM có sự tham gia của nhiều phòng ban và đặt mục tiêu nâng cao năng lực của công nhân vận hành, giảm thời gian chết dừng máy do sự cố.
Sau 3 tháng đầu tiên, Công ty đã thống kê được các nguyên nhân dừng máy. Điều này giúp công ty đưa ra giải pháp tức thời phù hợp để khắc phục. Từ 1/2019, công ty đã giám sát và giảm được thời gian dừng máy do sự cố. Đến tháng 2, công ty đã giảm được 5,8% thời gian dừng máy so với tháng 1/2019.
Tại Công ty TNHH Tân Huy Hoàng, thời gian đầu áp dụng TPM công ty đã xác định được 51 tổn thất, lãng phí trong sản xuất, tính toán về chi phí cho thấy công ty thất thoát khoảng 1,2 tỷ đồng/năm. Vì thế, công ty đã quyết định lựa chọn khởi động 5 đề tài cải tiến, trong đó có 2 đề tài cho thấy kết quả rõ ràng về mặt lợi ích là cải tiến “Giảm trọng lượng của 5 mã sản phẩm khó sản xuất” và cải tiến “Giảm thời gian xếp bông trong công đoạn sản xuất tấm panel”.
Với đề tài Giảm trọng lượng của 5 mã sản phẩm khó sản xuất, có 5 mã sản phẩm thường có trọng lượng vượt tiêu chuẩn hoặc ở cận trên của tiêu chuẩn. Khi áp dụng cải tiến, trọng lượng của một vài mã sản phẩm đã được đưa về mức tiêu chuẩn, thậm chí mức thấp hơn tiêu chuẩn nhưng vẫn đảm bảo chất lượng.
Với đề tài thứ 2, việc làm cữ dẫn hướng cho bông đi vào máy panel và thay đổi vị trí của sensor đã giúp giảm thời gian công nhân xếp bông lên máy từ 8 phút xuống còn 3 phút, lượng bông lỗi từ 10m/lần chạy giảm còn 2,5m/lần chạy.
Theo đánh giá, bên cạnh lợi ích về giảm lãng phí, việc áp dụng TPM cũng tạo ta giá trị khác cho DN là đã giúp phát động phong trào cải tiến tại phân xưởng cơ khí, tránh tình trạng cải tiến tự phát và không được ghi nhận như trước đây.
Tại Công ty TNHH Công nghiệp Trí Cường, chỉ trong thời gian ngắn, DN đã nhanh chóng tạo lập nền tảng cho 3 trụ cột triển khai với phạm vi áp dụng tại máy phay CNC 1-2, máy tiện CNC 2 thuộc phòng sản xuất số 1. Ngoài ra, Công ty đã thu được lợi ích về quản lý trực quan, tác phong nề nếp nhân viên, quản lý sản xuất và hiệu quả về mặt năng suất thiết bị.
Về hiệu quả năng suất, TCI đã giảm được thời gian chuyển đổi sản phẩm thông qua các cải tiến (giảm thời gian rà gá từ 21 phút xuống 15 phút) giúp nâng cao hiệu suất tổng thể thiết bị OEE của máy phay CNC từ 38% (tháng 11) lên 50% (tháng 12) và OEE máy tiện CNC từ 73% (tháng 11) lên 76% (tháng 12).
Về hiệu quả an toàn, việc hoạch định lại các dụng cụ cũng như tiêu chuẩn hóa các thao tác nên mặt bằng hợp lý và rộng rãi hơn, qua đó giúp công nhân di chuyển ít hơn từ đó tăng tính an toàn cho công nhân khi tham gia tác nghiệp...
Như vậy, việc áp dụng công cụ TPM đã mang lại hiệu quả rất tích cực cho DN, việc duy trì và nỗ lực mở rộng TPM sẽ mang lại các hiệu quả lớn hơn nữa về cải tiến năng suất, chất lượng, góp phần nâng cao hiệu quả sản xuất của doanh nghiệp trong dài hạn.